一、概述
每臺爐安裝一套正壓濃相氣力輸送系統,兩臺機組公用一套輸灰空壓機站。每臺爐的輸灰能力為38t/h,以滿足b-mcr 工況下燃用校核煤種時灰量的120%的出力裕量要求。每臺爐的輸灰系統入口通過膨脹節與省煤器灰斗閘板門、電除塵灰斗閘板門連接,共連接省煤器灰斗6個,電除塵灰斗32個。省煤器輸灰管線通過鋼支撐和抱箍固定在鍋爐鋼結構上,在電除塵處并入電除塵一、二電場輸灰母管管線,電除塵三四電場輸灰管線在末端倉泵出口處合并為一根輸灰管線。干灰儲存采用粗細灰分別貯存,每兩臺爐共用一座原灰庫、一座粗灰庫和一座細灰庫,每座灰庫的有效容積為1500m3。
飛灰輸送系統的控制室布置在兩臺爐電除塵器之間,飛灰輸送系統采用連續運行方式,飛灰輸送系統通過可編程控制器可以設置為根據出力自動運行方式或人為調整運行方式。 該每臺爐安裝一套正壓濃相氣力輸送系統,兩臺機組公用一套輸灰空壓機站。每臺爐的輸灰能力為38t/h,以滿足b-mcr 工況下燃用校核煤種時灰量的120%的出力裕量要干灰系統兩爐設一座輸灰空壓機站,每座輸灰空壓機站有四臺輸灰空壓機,設計為兩臺機組運行時,4臺空壓機3用1備。
該系統采用正壓濃相氣力輸灰,通過壓縮空氣將物料以柱狀形式進行輸送,輸送距離長,效率高,與傳統的稀相系統相比有比較明顯的技術優勢。
其優勢主要由以下四點:
1.系統簡單、安全、可靠。整套系統中除去倉泵圓頂閥外,沒有其它轉動部件,設備磨損小,維護費用低;
2.輸送速度較低,管道磨損較小,可以采用普通鋼管;
3.輸送物料濃度大,處理量大;
4.輸送系統全封閉的特性滿足日益提高的環保要求。
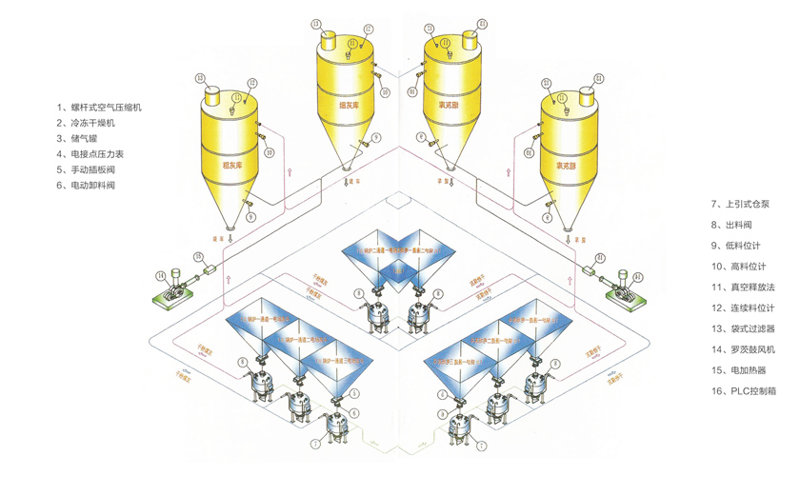
二、冬季輸灰故障及其治理方案
該正壓濃相氣力輸灰系統2016年9月投入生產,投產之初運行是平穩的,投產兩個月后,系統運行非常不順暢,最嚴重時電除塵四個電場有三個電場均報高料位,嚴重的影響電除塵的正常運行,甚至直接危及到機組的安全運行。經過設備治理和改造,系統和設備的穩定性明顯提高,在2017年徹底消除該隱患,確保機組在滿負荷下的長期穩定運行。本文將就其故障成因及其治理方案予以闡述,以期拋磚引玉。
1.干除灰系統故障現象
干灰系統自投產以來,多次發生輸灰不暢的事件,致使電除塵器各電場頻繁發生高料位報警,迫使電除塵各相關電場被迫停運,嚴重影響后續的脫硫系統的運行,造成吸收塔漿液中毒,脫硫效率下降。
2.造成電除塵電場退運
因該電廠涉及燃煤,燃煤的灰分較高,因干灰系統排灰不暢,大量的灰塵積存在灰斗中,灰斗的設計容量為滿負荷運行8小時的灰量,當灰斗裝滿后,灰塵會因電除塵振打而繼續堆積,逐漸堆積至極板和極線,致使二者短路,造成該電除塵電場退出運行。
3.造成吸收塔漿液中毒
正常情況下,煙氣自鍋爐排出后經過省煤器后進入空氣預熱器,而后進入靜電除塵器,經過靜電除塵器捕捉除塵后,進入增壓風機,之后進入吸收塔,經過煙氣脫硫后進入煙囪,排入大氣。
但是當電除塵電場因灰料位較高退運后,電場便失去了對煙氣的除塵效能,造成大量的含塵煙氣進入脫硫系統,對增壓風機的葉片、風機殼體造成沖刷、磨損,同時大量的含塵煙
氣進入吸收塔,使吸收塔的漿液中毒,降低了吸收塔的脫硫效率,使排放的煙氣中的粉塵和硫化物超標,對環境造成污染。這不符合當前的環保政策,也不符合排放要求。
4.干除灰系統故障的成因
在解體處理過程中發現灰管線內有大量灰塵沉積,灰管線截面的三分之二幾乎都是滿灰的。檢查供氣壓力是正常的,各管線疏通處理結束后,重新啟動該干灰輸送系統,檢查控制室輸灰曲線在系統運行初期是正常的,輸灰曲線逐漸的偏離正常的軌道,一般在啟動氣動干灰輸送系統持續3~4小時即再次發生該缺陷。
經多次排查后發現氣動干灰輸送系統各倉泵輔助流化風管路節流孔板處有水滴、冰屑,且節流孔被積灰堵塞,檢修初期現場工作人員沒有對此現象引起足夠的重視,其實這正是癥結所在。
正常的運行流程如下:輸灰空壓機制造的壓縮氣體暫存于三個儲氣罐中,由供氣聯絡母管分別對兩臺爐氣力干灰輸送系統供氣,壓縮空氣經管道過濾器至干灰系統倉泵壓縮空氣管路氣動門,在干灰系統輸送時,各倉泵氣動門打開,主輸灰管線壓縮空氣經逆止閥、節流孔板進入輸灰管線,各輔助輸灰壓縮空氣沿輔助流化風管路經節流孔板、逆止閥、氣化傘進入干灰倉泵,輔助干灰輸送。該循環結束后,干灰系統各倉泵壓縮空氣管路氣動門關閉,系統啟動下灰程序,開始下一個輸灰循環。
實際的輸灰運行中,由于輸灰空氣中含有較多水分,在低溫環境下,水分在管路內部凝結成水滴,甚至凝結成冰附著在管壁上,在干灰系統倉泵壓縮空氣管路氣動門開啟時,水滴會隨輸送氣沿節流孔板進入輔助風管路或者附著在節流孔板上,節流孔板上的節流孔直徑僅為3mm ,當關閉干灰系統倉泵壓縮空氣管路氣動門,停止輸送風時,灰塵有瞬間的回吸,灰塵與水滴就混合成灰漿,將節流孔堵塞。如果是脫落的冰晶可能就會瞬間堵塞節流孔板。從實際的解體中發現,節流孔板及以下的輔助風管路中灰塵堵塞較重,在節流孔板上方發生過整根管路被冰堵塞的情況
5.針對干除灰系統故障成因的解決方案
根據輸灰壓縮空氣含水較高的現象制定相應措施,首先要減少水分的來源,因空壓機房設在外圍,距離涼水塔較近,空氣濕度相對較大,受限于客觀條件,只能從除去輸灰壓縮空氣中的水分和防止輸灰壓縮空氣中的水分結露兩方面入手。主要從以下三個方面七項措施入手開展治理工作: 2.3.1 強化壓縮空氣疏水
輸灰壓縮空氣中的水分是造成干灰系統運行不暢的重要原因,如何降低輸灰壓縮空氣中的水分是治理氣力干除灰系統治理的重要內容之一。主要開展了以下三項措施:
5.1改進空壓機疏水措施
原空壓機疏水系統是浮球式自動疏水閥,其原理是利用積水的對閥體內部浮球的浮力,當積水達到一定高度時,浮力推動浮球從而打開疏水閥,當水泄出后,浮力降低,浮球落下,關閉自動疏水閥。
從實際情況觀察,自動疏水器的打開時間約為兩秒,兩次疏水的間隔時間約為15分鐘。 為強化疏水效果,更改為電磁疏水閥,通過時間設定,疏水周期間隔三分鐘,疏水時間為5秒,強化其疏水的頻次和疏水的時長,通過強制疏水,降低空壓機輸水系統的積水量,從而降低空壓機輸出的壓縮空氣的含水量。
5.2改進冷干機疏水措施
冷干機的冷凝水疏放方式原設計為人工疏水,空壓機房無專門值班員,需巡檢員定期巡檢時手動疏水,疏水時間間隔為2小時,疏水周期間隔偏長。
從現場的定期巡檢疏水情況看,在進行手動疏水時,冷凝水水量較大。
為強化冷干機的疏水效果,同樣改為電磁疏水閥,通過調整電磁閥動作時間,強化疏水的頻次和疏水的時長,降低冷干機的冷凝水量,減少其對輸灰壓縮空氣的影響。
5.3改進儲氣罐疏水頻次
儲氣罐的冷凝水疏放方式原設計為人工疏水,需巡檢員定期巡檢時手動疏水,原規程規定運行每班下班前疏水一次,疏水周期間隔偏長。
重新修訂規定,運行每班疏水兩次,時間間隔為4小時,完善巡檢路線,增加小神探巡檢點,巡檢記錄定點上傳。通過強化運行人員的巡檢疏水,減少儲氣罐中的積水,從而減少壓縮空氣的含水量。
5.4增加保溫措施
輸灰壓縮空氣系統原始設計中對管路未設計保溫,通過對現場的定期定點監測,該廠冬至期間一個月地面溫度約為-15℃左右,極端情況下曾測得-25℃。
在這種冬季低溫天氣條件下,壓縮空氣中的水分在管路內壁結露、凝結成冰都是很迅速的。所以增加保溫措施是十分必要的措施。
5.5增加室外儲罐的保溫措施
由于儲氣罐直接安裝在室外,在低溫天氣下,凝結水在儲氣罐罐底凝結成冰,曾多次發生儲氣罐無法輸出積水的狀況。
為此對儲氣罐整體進行保溫處理,從實際情況觀察,自罐體保溫工作整體完成后,管內積水沒有在發生結冰現象。
5.6增加室外輸灰空氣管路的保溫措施
室外的輸灰壓縮空氣管路沒有保溫措施,且管徑較細,鑒于此,對室外的輸灰壓縮空氣管路施加電伴熱帶+保溫巖棉的保溫措施,實際實施效果較好。
5.7增加疏水管路的電伴熱措施
儲氣罐的疏水管路閥門安裝在管路末端,壓縮空氣的冷凝水就會在輸水管路中凝結為冰,因此對此疏水管路自儲氣罐罐體底部出口開始敷設伴熱帶,同時外敷保溫巖棉,手動疏水閥門處將操作手柄引出,確保伴熱帶對閥體的加熱有效,消除罐內積水在管路中結冰的可能性。
5.8變更節流孔板材質
輸灰壓縮空氣中含水分較多,使輸灰系統的各節流孔板逐漸堵塞,輸灰管線輸灰效果降低,管線頻繁堵塞,維護工作量極大。
經深入分析,產生此類現象的主要原因為:當輸灰壓縮空氣經由節流孔板進入輸灰管道,節流孔板的節流孔直徑為3mm ,輸灰壓縮空氣通過節流孔板后由0.8mpa 降到不足0.3mpa ,輸灰壓縮空氣中的水分在通過金屬材質的節流孔板時直接結露或凝結,這一現象在模擬試驗中得到驗證。
針對以上原因,解決方案如下:
節流孔板屬于系統配置,通過節流孔板合理調整系統配氣,使氣灰配比最優化,節流孔板的配置不可變更。
金屬材料的導熱率極高,尤其是外界溫度較低時,壓縮空氣的水分凝結的更快。為此,需要一種耐磨且導熱率低的代替材料來替代金屬材料。
最終選定聚四氟乙烯板作為鋼板的替代品,通過現場安裝測試,聚四氟乙烯板材完全能夠勝任,聚四氟乙烯材質的節流板上僅有水滴,并無結冰現象。
通過以上方案的實施,解決了壓縮空氣中含水造成的干灰系統嚴重不暢的問題。對正壓濃相氣力輸灰系統的治理,安全的度過了之后的寒冷冬季,從抽樣檢查情況看,聚四氟乙烯板材的節流孔板在運行兩年后,其孔徑僅平均增大約35絲,是符合要求的。目前系統運行良好。正壓濃相氣力輸灰系統的治理和改造工作將是一個長期的、持續的工作,需要在做好各項定檢、定維工作的前提下不斷的改進。